Papers by Amir Abdollahpoor
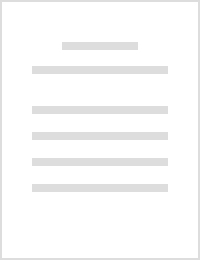
It is known that tailoring a hot stamping part, to achieve locally graded properties, can improve... more It is known that tailoring a hot stamping part, to achieve locally graded properties, can improve the crash behavior. Depending on the role of the structural part (carrying either bending or axial crash load), the best position for the local regions with lower strength and higher ductility can be different. The distribution of these local regions and their mechanical properties affects the crash behavior of the part in each loading case and therefore can be effectively designed to improve the crash performance. To investigate these effects and examine the improvement possibilities, a numerical thermal-mechanical-metallurgical model of a hot stamping process and a representa-tive side impact crash model were created and analysed. The hot stamping model was used to predict the consequent phase fractions and mechanical properties of tailored hot stamping parts produced with different tailoring scenarios. In the metallurgical model, a modified phase trans-formation model based on Scheil’s additive principle was incorporated. The geometry and mesh of the stamped part was exported to a crash numerical model with a 3-point bending configura-tion. A constitutive model was used to define the plastic behavior of the stamped part correspond-ing to different hardness values. Various possibilities in locally positioning the high strength or high ductility zones of material were examined. The results show that the positioning of the soft zones has a more significant effect on the crash performance than the variation in their mechanical properties of these soft zones.

The optimization of circular aluminum tube as crash energy absorber that usually is used in
auto... more The optimization of circular aluminum tube as crash energy absorber that usually is used in
automobile and train structures is studied in this paper. To simulate a complicated behavior of this kind of
crash problem, an explicit finite element software LS DYNA is used. In order to validate the finite element
modeling, some FE results have been compared with experimental test results. The Response Surface
Method (RSM) which does not require sensitivity analysis of the crushing behavior is applied to
maximize the energy absorption and specific energy absorption with the mean crash force as constraint.
The D-Optimal design of experiments has been used to reduce the number of needed points for approximation
in the Response Surface Method. Design of experiments has been done by the Design Expert
software that provides highly efficient design of experiments and optimization. The optimization process
has been repeated until the convergence criteria are satisfied.

A thin-walled cylindrical tube, when subjected to an axial load, will be
folded and will absorb ... more A thin-walled cylindrical tube, when subjected to an axial load, will be
folded and will absorb an impact energy. In the design of a frontal cylindrical
tube for absorbing the kinetic energy during car accidents, there were a lot of
theoretical and experimental researches that have dened the characteristics
of the tube during cars accidents. After studying most of these researches, it
was found that the theoretical approach usually simplied the problem and
could not be used condently in design. Experimental approach usually faced
diculty when the material was changed.
In this paper, a computer simulation program joined with the response
surface methodology was planned to nd the tube characteristics in axial impacts.
The problem parameters were dimensional measures of an aluminium
circular tube including thickness, diameter and length. The output of the work
was to nd the variation of the absorbed energy and mean crash force of the
tube with the parameters in the applicable automotive ranges. Also, our results
were compared with some available theoretical approaches.
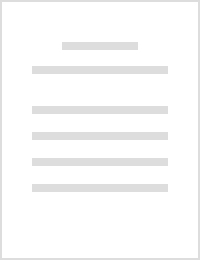
Hot stamping is a thermal-mechanical-metallurgical process to produce vehicle body components wit... more Hot stamping is a thermal-mechanical-metallurgical process to produce vehicle body components with high strength and complex geometries. In this process, hot sheet metal is formed within a die and cooled down at the same time. The cooling rates are critical to the final microstructure and thus the final mechanical properties of the part in service (strength, ductility, energy absorption ability). Tailored hot stamping parts – where the cooling rates are locally chosen to achieve structures with graded properties – allow local modification of final mechanical properties to provide high energy absorption and low intrusion from a single structural part simultaneously. This paper is focussed on predicting the crash response of the tailored hot stamping components. A numerical model of a tailored hot stamping process is used to predict the post-formed properties, including hardness and thickness distribution over the part. Then, a numerical model of the post-formed part under the crash loading is created to predict the crash response. The effects of the variations in post-formed properties on the crash response are investigated.

Hot stamping is an innovative forming process for the production of vehicle body parts with compl... more Hot stamping is an innovative forming process for the production of vehicle body parts with complicated geometries and high strength. In this process, hot sheet metal is formed within a die and cooled down at the same time. The cooling rates are critical to the final microstructure and thus the final mechanical properties of the part in service (strength, ductility, energy absorption ability). Therefore, an accurate model that can predict the thermo-mechanical-metallurgical characteristics of the process is increas-ingly important. In this paper, a thermo-mechanical finite element model of hot stamping is created and a modified phase transformation model based on Scheil’s additive principle has been applied. The comparison between the modeling and experiment shows that the modified phase transformation model coupled with the incubation time provides higher accuracy on the simulation of transformation kinetics history. In the stamp-ing process, the effect of different die materials and increasing the die temperature to reduce the sheet cool-ing rate is analyzed in this paper. This work demonstrates the application of the combined thermo-mechanical-metallurgical model in hot stamping. Additionally, the results provide insights into the use of locally differentiated cooling rates, either via local die material changes or selective heating, to produce tailored mechanical properties in hot stamped components.

Advanced Materials Research, Oct 2014
The final mechanical properties of hot stamped components are affected by many process and materi... more The final mechanical properties of hot stamped components are affected by many process and material parameters due to the multidisciplinary nature of this thermal-mechanical-metallurgical process. The phase transformation, which depends on the temperature field and history, determines the final microstructure and consequently the final mechanical properties. Tailored hot stamping parts -where the cooling rates are locally chosen to achieve structures with graded properties -has been increasingly adopted in the automotive industry. Robustness of the final part properties is more critical than in the conventional hot stamping. In this paper, the robustness of a tailored hot stamping set-up is investigated. The results show that tailored hot stamping is very sensitive to tooling temperature, followed by latent heat radiation emissivity, and convection film coefficient. Traditional hot stamping has higher robustness compared to tailored hot stamping, with respect to the stamped component's final material properties (i.e. phase fraction, hardness).

Journal of Materials Processing Technology, 2015
Robustness studies for relevant process conditions of tailored hot stamping.Thermal–mechanical–me... more Robustness studies for relevant process conditions of tailored hot stamping.Thermal–mechanical–metallurgical modelling of the hot stamping process.Conventional hot stamping is highly robust relative to tailored hot stamping.Tailored hot stamping process is highly sensitive to input process parameters.Tailored hot stamping is more robust using low conductive tooling.The final mechanical properties of hot stamped components are affected by many process and material parameters due to the multidisciplinary nature of this thermal–mechanical–metallurgical process. The phase transformation, which depends on the temperature field and history, determines the final microstructure and consequently the final mechanical properties. Tailored hot stamping parts – where the cooling rates are locally chosen to achieve structures with graded properties – has been increasingly adopted in the automotive industry. In this case, the robustness of final part properties is more critical than in the conventional hot stamping parts, where the part is fully quenched. In this study, a wide range of input parameters in a generalized hot stamping model have been investigated, examining the effect on the temperature history and resulting final material properties. A generic thermo-mechanical finite element model of hot stamping was created and a modified phase transformation model, based on Scheil's additive principle, has been applied. The comparison between modeling and experiments shows that the modified phase transformation model coupled with the incubation time provides higher accuracy on the simulation of transformation kinetics history. The robustness of four conditions relevant to tailored hot stamping was investigated: heated tooling (with low and high tool conductance), air cooling, and conventional hot stamping. The results show the high robustness of the conventional hot stamping compared to tailored hot stamping, with respect to the stamped component's final material properties (i.e. phase fraction and hardness). Furthermore, tailored hot stamping showed higher robustness when low conductivity tools are used relative to high conductivity tools.
International Journal of Crashworthiness, 2009
Axial crash of thin-walled circular aluminum tubes is investigated in this study. These kinds of ... more Axial crash of thin-walled circular aluminum tubes is investigated in this study. These kinds of tubes usually are used in automobile and train structures to absorb the impact energy. An explicit finite element method (FEM) is used to model and analyse the behaviour. Formulation of the energy absorption and the mean crash force in the range of variables is presented using design of experiments (DOE) and response surface method (RSM). Comparison with experimental tests has been accomplished in some results for validation. Also, comparison with the analytical aspect of this problem has been done. Mean crash force has been considered as a constraint as its value is directly related to the crash severity and occupant injury. The results show that the triggering causes a decrease in the maximum force level during crash.
Uploads
Papers by Amir Abdollahpoor
automobile and train structures is studied in this paper. To simulate a complicated behavior of this kind of
crash problem, an explicit finite element software LS DYNA is used. In order to validate the finite element
modeling, some FE results have been compared with experimental test results. The Response Surface
Method (RSM) which does not require sensitivity analysis of the crushing behavior is applied to
maximize the energy absorption and specific energy absorption with the mean crash force as constraint.
The D-Optimal design of experiments has been used to reduce the number of needed points for approximation
in the Response Surface Method. Design of experiments has been done by the Design Expert
software that provides highly efficient design of experiments and optimization. The optimization process
has been repeated until the convergence criteria are satisfied.
folded and will absorb an impact energy. In the design of a frontal cylindrical
tube for absorbing the kinetic energy during car accidents, there were a lot of
theoretical and experimental researches that have dened the characteristics
of the tube during cars accidents. After studying most of these researches, it
was found that the theoretical approach usually simplied the problem and
could not be used condently in design. Experimental approach usually faced
diculty when the material was changed.
In this paper, a computer simulation program joined with the response
surface methodology was planned to nd the tube characteristics in axial impacts.
The problem parameters were dimensional measures of an aluminium
circular tube including thickness, diameter and length. The output of the work
was to nd the variation of the absorbed energy and mean crash force of the
tube with the parameters in the applicable automotive ranges. Also, our results
were compared with some available theoretical approaches.
automobile and train structures is studied in this paper. To simulate a complicated behavior of this kind of
crash problem, an explicit finite element software LS DYNA is used. In order to validate the finite element
modeling, some FE results have been compared with experimental test results. The Response Surface
Method (RSM) which does not require sensitivity analysis of the crushing behavior is applied to
maximize the energy absorption and specific energy absorption with the mean crash force as constraint.
The D-Optimal design of experiments has been used to reduce the number of needed points for approximation
in the Response Surface Method. Design of experiments has been done by the Design Expert
software that provides highly efficient design of experiments and optimization. The optimization process
has been repeated until the convergence criteria are satisfied.
folded and will absorb an impact energy. In the design of a frontal cylindrical
tube for absorbing the kinetic energy during car accidents, there were a lot of
theoretical and experimental researches that have dened the characteristics
of the tube during cars accidents. After studying most of these researches, it
was found that the theoretical approach usually simplied the problem and
could not be used condently in design. Experimental approach usually faced
diculty when the material was changed.
In this paper, a computer simulation program joined with the response
surface methodology was planned to nd the tube characteristics in axial impacts.
The problem parameters were dimensional measures of an aluminium
circular tube including thickness, diameter and length. The output of the work
was to nd the variation of the absorbed energy and mean crash force of the
tube with the parameters in the applicable automotive ranges. Also, our results
were compared with some available theoretical approaches.