Thesis Chapters by Benjamin Woods

This research focuses on the development of an active rotor system capable of primary control and... more This research focuses on the development of an active rotor system capable of primary control and vibration reduction for rotorcraft. The objective is to investigate the feasibility of a novel Trailing Edge Flap (TEF) actuation system driven by Pneumatic Artificial Muscles (PAMs). A significant design effort led to a series of experimental apparatuses which tested various aspects of the performance of the actuators themselves and of TEF systems driven by them. Analytical models were developed in parallel to predict the quasistatic and dynamic behavior of these systems.
Initial testing of a prototype blade section with an integrated PAM driven TEF proved the viability of the concept through successful benchtop testing under simulated M = 0.3 loading and open jet wind tunnel tests under airspeeds up to M = 0.13. This prototype showed the ability of PAM actuators to generate significant flap deflections over the bandwidth of interest for primary control and vibration reduction on a rotorcraft. It also identified the importance of high pneumatic system mass flow rate for maintaining performance at higher operating frequencies.
Research into the development and improvement of PAM actuators centered around a new manufacturing technique which was invented to directly address the weaknesses of previous designs. Detailed finite element model (FEM) analysis of the design allowed for the mitigation of stress concentrations, leading to increased strength. Tensile testing of the swaged actuators showed a factor of safety over 5, and burst pressure testing showed a factor of safety of 3. Over 120,000,000 load cycles were applied to the actuators without failure. Characterization testing before, during, and after the fatigue tests showed no reduction in PAM performance.
Wind tunnel testing of a full scale Bell 407 blade retrofitted with a PAM TEF system showed excellent control authority. At the maximum wind tunnel test speed of M = 0.3 and a derated PAM operating pressure of 28 psi, 18.8° half-peak-to-peak flap deflections were achieved at 1/rev (7 Hz), and 17.1° of half-peak-to-peak flap deflection was still available at 5/rev (35 Hz). A quasistatic system model was developed which combined PAM forces, kinematics and flap aerodynamics to predict flap deflection amplitudes. This model agreed well with experimental data.
Whirl testing of a sub-span whirl rig under full scale loading conditions showed the ability of PAM TEF systems to operate under full scale levels of centrifugal (CF), aerodynamic, and inertia loading. A commercial pneumatic rotary union was used to provide air in the rotating frame. Extrapolation of the results to 100% of CF acceleration predicts 15.4° of half-peak-to-peak flap deflection at 1/rev (7 Hz), and 7.7° of half-peak-to-peak flap deflection at 5/rev (35 Hz).
A dynamic model was developed which successfully predicted the time domain behavior of the PAM actuators and PAM TEF system. This model includes control valve dynamics, frictional tubing losses, pressure dynamics, PAM forces, mechanism kinematics, aerodynamic hinge moments, system stiffness, damping, and inertia to solve for the rotational dynamics of the flap.
Control system development led to a closed loop control system for PAM TEF systems capable of tracking complex, multi-sinusoid flap deflections representative of a combined primary control and vibration reduction flap actuation scheme.
This research shows the promise that PAM actuators have as drivers for trailing edge flaps on active helicopter rotors. The robustness, ease of integration, control authority and tracking accuracy of these actuators have been established, thereby motivating further research.
Papers by Benjamin Woods
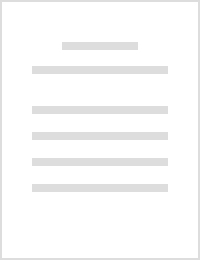
Journal of Dynamic Systems Measurement and Control
Pneumatic artificial muscles (PAMs) are comprised of an elastomeric bladder surrounded by a braid... more Pneumatic artificial muscles (PAMs) are comprised of an elastomeric bladder surrounded by a braided mesh sleeve. When the bladder is inflated, the actuator may either contract or extend axially, with the direction of motion dependent on the orientation of the fibers in the braided sleeve. Contractile PAMs have excellent actuation characteristics, including high specific power, specific work, and power density. Unfortunately, extensile PAMs exhibit much reduced blocked force, and are prone to buckling under axial compressive loading. For applications in which extensile motion and compressive force are desired, the push-PAM actuator introduced here exploits the operational characteristics of a contractile PAM, but changes the direction of motion and force by employing a simple internal mechanism using no gears or pulleys. Quasi-static behavior of the push-PAM was compared to a contractile PAM for a range of operating pressures. Based on these data, the push-PAM actuator can achieve fo...
48th AIAA/ASME/ASCE/AHS/ASC Structures, Structural Dynamics, and Materials Conference, 2007
50th AIAA/ASME/ASCE/AHS/ASC Structures, Structural Dynamics, and Materials Conference, 2009
Morphing aircraft reconfigure themselves to optimize flight performance for various and substanti... more Morphing aircraft reconfigure themselves to optimize flight performance for various and substantially different mission objectives. Research and simulation studies have shown the wide variety of performance benefits afforded by morphing technologies, but there have historically been ...
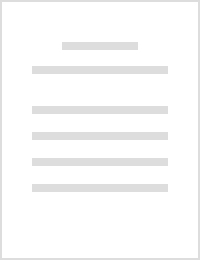
Volume 1: 21st Biennial Conference on Mechanical Vibration and Noise, Parts A, B, and C, 2007
ABSTRACT This research investigates the feasibility of using Pneumatic Artificial Muscles (PAMs) ... more ABSTRACT This research investigates the feasibility of using Pneumatic Artificial Muscles (PAMs) to drive a rotor blade Trailing Edge Flap (TEF) for primary control and/or vibration reduction. Specifically, this work investigates the effects of operating these compliant, pneumatic actuators under the high CF loading typical of a helicopter rotor blade. A prototype TEF actuation system was designed and built. It was tested in a vacuum whirl chamber over a range of centrifugal accelerations. Bi-directional actuation was performed to track changes in system performance with increasing CF field. Additionally, testing was performed under different levels of torsional spring loading to simulate aerodynamic hinge moment effects. Results of these tests motivated a second experiment wherein the effects of CF loading on the PAMs themselves are isolated from the rest of the system. This was accomplished by fixing the ends of PAM and performing blocked force testing over a range of centrifugal accelerations. Taken together, these tests show that chordwise PAM actuators are capable of operating under high CF loading with only minor losses in performance. Additionally, the need for careful design of actuation and flap system components for operation in this harsh environment is reiterated.
Recent Advances in Aircraft Technology, 2012
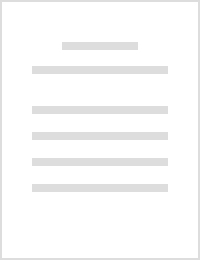
Aerospace Science and Technology, 2015
ABSTRACT A variable camber morphing airfoil with compliant ribs and flexible composite skins is s... more ABSTRACT A variable camber morphing airfoil with compliant ribs and flexible composite skins is studied in a hierarchical modeling framework. The key requirements of a variable camber morphing airfoil are the flexible skin, compliant internal structure and a lightweightactuation system. A biologically inspired, internal structure is adapted to produce continuous camber morphing. The conflicting requirements of the morphing skin, namely low in-plane stiffness and high out-of-plane bending stiffness, are metby designing the composite with curvilinear fiber paths. A coupled aeroelastic simulation and optimization of the proposed 2-D morphing airfoil is computationally complex. Hierarchical computational models of the morphing airfoil are used to decouple the complaint ribs and airfoil skin. In the first level of hierarchy, a fluid-structure interaction is performed with the homogenizedbeam model of the compliant rib structure and 2-D panel method. In the second level, a finite element model of the camber morphing skin is developed with representative boundary conditions. A multi-objective optimization framework is developed to find the optimal curvilinear fiber paths of the morphing skin to meet the airfoil geometric shape and actuation requirements of the first level. The optimal results show that a significant camber variation and significant changes in aerodynamic properties can be achieved with the compliant skin and airfoil structure considered in this study. The hierarchical modeling framework of the camber morphing airfoil discussed in this paper enhances theoretical understanding of each sub-system and reduces the computational costs.
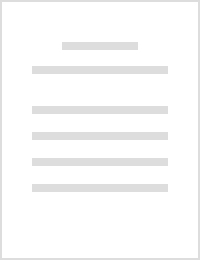
Journal of Intelligent Material Systems and Structures - J INTEL MAT SYST STRUCT, 2011
Recent advancements in actuator technology suggest that the implementation of reliable, high powe... more Recent advancements in actuator technology suggest that the implementation of reliable, high power-to-weight ratio pneumatic actuation systems is now possible for robotic platforms. Existing robotic manipulator arms for casualty extraction and patient placement use hydraulic actuation, whereas related robotic prosthetic devices typically use heavy actuator motors. We have developed an alternative solution that employs pneumatic artificial muscles (PAMs). The goal of this study is to identify requirements for a lightweight, high-force robotic manipulator, design the system for heavy lifting capability, and assemble a prototype arm. Following characterization and comparison of different-sized PAM actuators, a proof-of-concept manipulator was constructed. A quasi-static model for the PAM actuators was applied to the system, which includes the Gaylord force, as well as non-linear elastic energy storage. Experimental testing was performed to measure the joint torque and dynamic response ...
Journal of Intelligent Material Systems and Structures, 2012
Page 1. Article Journal of Intelligent Material Systems and Structures 0(0) 1–14 Ó The Author(s) ... more Page 1. Article Journal of Intelligent Material Systems and Structures 0(0) 1–14 Ó The Author(s) 2011 Reprints and permissions: sagepub.co.uk/journalsPermissions.nav DOI: 10.1177/1045389X11431743 jim.sagepub.com Design and testing of a high-specific ...
… and Automation, 2009 …, 2009
Page 1. Abstract This paper presents the dynamic modeling of Mckibben pneumatic artificial muscl... more Page 1. Abstract This paper presents the dynamic modeling of Mckibben pneumatic artificial muscles. The air flow model of a valve orifice and the air volume model of a pneumatic muscle are incorporated into the proposed ...

Aerospace Science and Technology, 2013
This paper presents the Zigzag wingbox concept that allows the wing span to be varied by 44% (22%... more This paper presents the Zigzag wingbox concept that allows the wing span to be varied by 44% (22% extension and 22% retraction). The Zigzag wingbox consists of a rigid part and a morphing part. The rigid part is a semi-monocoque construction that houses the fuel tank and transfers the aerodynamic loads from the morphing part to the fuselage. The morphing part consists of various morphing partitions where in each partition there are two spars each consisting of two beams hinged together. Each morphing partition is covered by flexible skin and is bounded by two ribs through which the spars are connected. The ribs transfer the loads between the spars of adjacent morphing partitions and serves as the main structure to which the flexible skins are to be attached. The Zigzag wingbox concept is then incorporated in the rectangular wing of a medium altitude long endurance (MALE) UAV to enhance its operational performance and provide roll control. Equivalent modelling and preliminary sizing of the concept are performed to assess its feasibility and quantify its potential benefits.
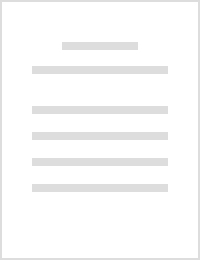
This article discusses the development, analysis, and testing of a mechanism designed to passivel... more This article discusses the development, analysis, and testing of a mechanism designed to passively balance the energy requirements of mechanical systems and smart structures in order to reduce the size and weight of their actuation systems and to minimize the associated energy consumption. This passive energy balance is achieved by coupling a negative stiffness mechanism to the positive stiffness of the mechanical system being driven, thereby creating a net zero stiffness system which can be actuated with minimal energy requirements. The negative stiffness mechanism proposed here uses a cable spooling around a spiral-shaped pulley to convert decreasing forces in a pre-stretched linear extension spring into increasing torque output, thereby creating a torsional spring with negative output stiffness. An analytical model of the system was developed, and the geometry of the spiral pulley was optimized for a representative design case. An experimental demonstrator was then built and tested, confirming the ability of the concept to drastically reduce torque and energy required to actuate a representative load.
23nd AIAA/AHS Adaptive Structures Conference, 2015

This work introduces a new span morphing concept under development at Swansea University. Known ... more This work introduces a new span morphing concept under development at Swansea University. Known as the Adaptive Aspect Ratio wing, this concept couples a compliant skin material to a mechanism based internal structure to create a morphing wing capable of significant changes in span and aspect ratio. The four key technologies of the concept, namely the elastomeric matric composite skin, the telescoping spar, the sliding ribs and the strap drive, are first introduced and discussed. The compliant skin is established to be the dominant component in the overall design of this concept, requiring careful balancing between in-plane actuation force requirements and out-of-plane stiffness under aerodynamic loading. An initial skin design optimization exercise is then carried out using analytical models of the skin’s behaviour, providing significant insight into the interplay between the various parameters of the skin design.

A strongly coupled, partitioned fluid–structure interaction analysis is introduced which allows f... more A strongly coupled, partitioned fluid–structure interaction analysis is introduced which allows for calculation of the deformed equilibrium shape and actuation requirements of the Fish Bone Active Camber mechanism under quasi-static aerodynamic loading. The Fish Bone Active Camber mechanism has recently been introduced as a high authority morphing camber architecture with a broad range of applications; including fixed wing aircraft, helicopters, wind turbines, and tidal stream turbines. This design employs a biologically inspired compliant structure to create continuous changes in airfoil camber and aerodynamic properties. The structure consists of a thin chordwise bending beam spine with stringers branching off to connect it to a pre-tensioned Elastomeric Matrix Composite skin surface. An actuation system mounted in a rigid D-spar induces bending moments on the spine through an antagonistic pair of tendons in a manner similar to natural musculature systems. The low bending stiffness of the primary structure, high stiffness of the tendons, and the large changes in aerodynamic loading while morphing necessitate a fully coupled fluid–structure interaction analysis for determination of the static equilibrium at different operating conditions. An Euler–Bernoulli beam theory based analytical model of the structure is introduced. Aerodynamic pressure distributions on the skin surface are found using XFOIL software, which couples a panel method with a viscous boundary layer solver. Finally, the tendons are modeled as linear stiffness elements whose internal strains are found from Euler–Bernoulli theory and whose axial forces create bending moments on the spine at their discrete mounting points. Convergence of the FSI code is stabilized through incorporation of relaxation parameters to the tendon moments and deflected shape.

Presented at the Royal Aeronautical Society Applied Aerodynamics Conference, 22/7/2014, Bristol, UK
This paper presents a comparison of two different aerodynamic analysis methods for active camber ... more This paper presents a comparison of two different aerodynamic analysis methods for active camber morphing airfoils. Morphing camber airfoil concepts have for a long time been popular subjects of study. Both lower fidelity panel methods and higher fidelity computational fluid dynamics software have been extensively employed in previous work, but little direct comparison exists between the two. To this end, this paper compares a low-fidelity panel method, XFOIL, against OpenFOAM, a high-fidelity computational fluid dynamics code. A series of 2D analyses encompassing a range of morphing camber shapes and operating conditions are analyzed. The impact of changing angle of attack, start location of morphing, amount of morphing and Reynolds number on the predictions is shown. The codes compare well over a wide range of configurations, although higher angles of attack and larger camber changes lead to increased disparity.

Journal of Intelligent Material Systems and Structures, May 2014
This work presents comparative experimental investigations into the aerodynamics of the recently ... more This work presents comparative experimental investigations into the aerodynamics of the recently proposed Fish Bone Active Camber morphing structure. This novel, biologically inspired concept consists of four main elements: a compliant skeletal core, a pre-tensioned elastomeric matrix composite skin, an antagonistic pair of tendons coupled to a nonbackdriveable spooling pulley as the driving mechanism, and a non-morphing main spar. The Fish Bone Active Camber concept is capable of generating large changes in airfoil camber and is therefore proposed as a high-authority morphing solution for fixed-wing aircraft, helicopters, wind turbines, tidal stream turbines, and tilt-rotors. This testing compares a baseline airfoil employing a conventional trailing edge flap to a continuous morphing trailing edge using the Fish Bone Active Camber concept. Testing is performed in the low-speed wind tunnel at Swansea University over a range of camber deformations and angles of attack. Both approaches are capable of generating similar levels of lift coefficient; however, comparison of the drag results shows a significant reduction for the Fish Bone Active Camber geometry. While purely two-dimensional flow was not achieved due to restrictions of the tunnel, the two airfoils operated in similar flow environments, allowing for a direct comparison between the two. Over the range of angles of attack typically used in fixed and rotary wing applications, improvements in the maximum obtainable lift-to-drag ratio on the order of 20%-25% are shown.

AIAA Journal
Morphing aircraft concepts require powerful, compact and lightweight actuators in order to realiz... more Morphing aircraft concepts require powerful, compact and lightweight actuators in order to realize the significant changes in shape and aerodynamics desired. One source of inefficiency and lost performance common to all types of actuators is the mismatch between the force versus stroke profile available from the actuator and that required by the load. This work investigates a novel spiral spooling pulley mechanism that allows for kinematic tailoring of the actuator force profile to better match the force required to drive a given load. To show the impact of kinematic tailoring on actuator efficiency, a representative case study is made of a Pneumatic Artificial Muscle driven morphing camber airfoil employing the Fish Bone Active Camber concept. By using an advanced spiral pulley kinematic mechanism, the actuator force profile is successfully tailored to match that required, with an additional torque margin added to account for any unmodeled effects. Genetic algorithm optimization is used to select the geometric parameters of the spiral pulley that maximize energy efficiency of the actuator while ensuring it is able to produce the required torque levels. The performance of the optimized spiral pulley is compared to a baseline case employing an optimized circular pulley which does not alter the shape of the actuator force profile to show the performance improvement provided by the kinematic tailoring.
Uploads
Thesis Chapters by Benjamin Woods
Initial testing of a prototype blade section with an integrated PAM driven TEF proved the viability of the concept through successful benchtop testing under simulated M = 0.3 loading and open jet wind tunnel tests under airspeeds up to M = 0.13. This prototype showed the ability of PAM actuators to generate significant flap deflections over the bandwidth of interest for primary control and vibration reduction on a rotorcraft. It also identified the importance of high pneumatic system mass flow rate for maintaining performance at higher operating frequencies.
Research into the development and improvement of PAM actuators centered around a new manufacturing technique which was invented to directly address the weaknesses of previous designs. Detailed finite element model (FEM) analysis of the design allowed for the mitigation of stress concentrations, leading to increased strength. Tensile testing of the swaged actuators showed a factor of safety over 5, and burst pressure testing showed a factor of safety of 3. Over 120,000,000 load cycles were applied to the actuators without failure. Characterization testing before, during, and after the fatigue tests showed no reduction in PAM performance.
Wind tunnel testing of a full scale Bell 407 blade retrofitted with a PAM TEF system showed excellent control authority. At the maximum wind tunnel test speed of M = 0.3 and a derated PAM operating pressure of 28 psi, 18.8° half-peak-to-peak flap deflections were achieved at 1/rev (7 Hz), and 17.1° of half-peak-to-peak flap deflection was still available at 5/rev (35 Hz). A quasistatic system model was developed which combined PAM forces, kinematics and flap aerodynamics to predict flap deflection amplitudes. This model agreed well with experimental data.
Whirl testing of a sub-span whirl rig under full scale loading conditions showed the ability of PAM TEF systems to operate under full scale levels of centrifugal (CF), aerodynamic, and inertia loading. A commercial pneumatic rotary union was used to provide air in the rotating frame. Extrapolation of the results to 100% of CF acceleration predicts 15.4° of half-peak-to-peak flap deflection at 1/rev (7 Hz), and 7.7° of half-peak-to-peak flap deflection at 5/rev (35 Hz).
A dynamic model was developed which successfully predicted the time domain behavior of the PAM actuators and PAM TEF system. This model includes control valve dynamics, frictional tubing losses, pressure dynamics, PAM forces, mechanism kinematics, aerodynamic hinge moments, system stiffness, damping, and inertia to solve for the rotational dynamics of the flap.
Control system development led to a closed loop control system for PAM TEF systems capable of tracking complex, multi-sinusoid flap deflections representative of a combined primary control and vibration reduction flap actuation scheme.
This research shows the promise that PAM actuators have as drivers for trailing edge flaps on active helicopter rotors. The robustness, ease of integration, control authority and tracking accuracy of these actuators have been established, thereby motivating further research.
Papers by Benjamin Woods
Initial testing of a prototype blade section with an integrated PAM driven TEF proved the viability of the concept through successful benchtop testing under simulated M = 0.3 loading and open jet wind tunnel tests under airspeeds up to M = 0.13. This prototype showed the ability of PAM actuators to generate significant flap deflections over the bandwidth of interest for primary control and vibration reduction on a rotorcraft. It also identified the importance of high pneumatic system mass flow rate for maintaining performance at higher operating frequencies.
Research into the development and improvement of PAM actuators centered around a new manufacturing technique which was invented to directly address the weaknesses of previous designs. Detailed finite element model (FEM) analysis of the design allowed for the mitigation of stress concentrations, leading to increased strength. Tensile testing of the swaged actuators showed a factor of safety over 5, and burst pressure testing showed a factor of safety of 3. Over 120,000,000 load cycles were applied to the actuators without failure. Characterization testing before, during, and after the fatigue tests showed no reduction in PAM performance.
Wind tunnel testing of a full scale Bell 407 blade retrofitted with a PAM TEF system showed excellent control authority. At the maximum wind tunnel test speed of M = 0.3 and a derated PAM operating pressure of 28 psi, 18.8° half-peak-to-peak flap deflections were achieved at 1/rev (7 Hz), and 17.1° of half-peak-to-peak flap deflection was still available at 5/rev (35 Hz). A quasistatic system model was developed which combined PAM forces, kinematics and flap aerodynamics to predict flap deflection amplitudes. This model agreed well with experimental data.
Whirl testing of a sub-span whirl rig under full scale loading conditions showed the ability of PAM TEF systems to operate under full scale levels of centrifugal (CF), aerodynamic, and inertia loading. A commercial pneumatic rotary union was used to provide air in the rotating frame. Extrapolation of the results to 100% of CF acceleration predicts 15.4° of half-peak-to-peak flap deflection at 1/rev (7 Hz), and 7.7° of half-peak-to-peak flap deflection at 5/rev (35 Hz).
A dynamic model was developed which successfully predicted the time domain behavior of the PAM actuators and PAM TEF system. This model includes control valve dynamics, frictional tubing losses, pressure dynamics, PAM forces, mechanism kinematics, aerodynamic hinge moments, system stiffness, damping, and inertia to solve for the rotational dynamics of the flap.
Control system development led to a closed loop control system for PAM TEF systems capable of tracking complex, multi-sinusoid flap deflections representative of a combined primary control and vibration reduction flap actuation scheme.
This research shows the promise that PAM actuators have as drivers for trailing edge flaps on active helicopter rotors. The robustness, ease of integration, control authority and tracking accuracy of these actuators have been established, thereby motivating further research.