Papers by Robert Leishear
OpShow22, 2022
Water System Operators Can Stop Water Main Breaks. Nearly all water main breaks are caused by wat... more Water System Operators Can Stop Water Main Breaks. Nearly all water main breaks are caused by water hammers. Slow valve and hydrant operations can stop water hammers. Operators can stop water main breaks.
Water Main Breaks are a Trillion Dollar Wreck. There are $15 billion per year in U.S. and Canadian water main breaks. 250,000 water main breaks per year in U.S. and Canada. Replacement costs are $1 million per mile. $1 trillion in water main breaks in the next 25 years.

Water hammer pressure waves induce oscillating bands of high stresses along pipes, where fatigue ... more Water hammer pressure waves induce oscillating bands of high stresses along pipes, where fatigue corrosion accelerates at bands of localized high stress. Coined as tiger stripes, fatigue corrosion forms at nearly equidistant locations along the bore of piping. For this study, as manufactured A106 carbon steel piping, with intact mill scale, was examined both visually and with a scanning electron microscope (SEM, Zeiss, Gemini 500). The piping for this study was damaged by water hammer with thousands of scratch-like visible cracks with coupled corrosion, and millions of microscopic cracks were discovered during this research. Some piping experienced corrosion bands, and some did not, where these differences in corrosion mechanics are discussed in a Part I of this series. For comparison to piping fatigue corrosion, an as-manufactured, carbon steel flat bar with intact mill scale was investigated. The mill scale was removed with a grinder, and this sample was corroded in a saturated salt solution at 20 °C. As expected, the base metal was not significantly cracked, even after extensive corrosion. However, the corrosion products, or rust deposits, were cracked in numerous locations. In short, water hammer cracks piping, and cracks induce crevice corrosion to shorten the lives of piping systems. This study provides an extensive SEM photographic library to concisely explain and understand fatigue corrosion. Although I reviewed far more photographs than are presented here, one goal of this work is to permit the reader to comprehensively visualize the results that were discovered. What I see is what I want others to see, where this work is applicable to corrosion, piping, structural, and fluids engineering.

Research was completed at Savannah River National Laboratory (SRNL) to investigate processes rela... more Research was completed at Savannah River National Laboratory (SRNL) to investigate processes related to the blending of radioactive, liquid waste, salt solutions in 4920 cubic meter, 25.9 meter diameter storage tanks. One process was the blending of large salt solution batches (up to 1135 – 3028 cubic meters), using submerged centrifugal pumps. A second process was the disturbance of a settled layer of solids, or sludge, on the tank bottom. And a third investigated process was the settling rate of sludge solids if suspended into slurries by the blending pump. To investigate these processes, experiments, CFD models (computational fluid dynamics), and theory were applied. Experiments were performed using simulated, non-radioactive, salt solutions referred to as supernates, and a layer of settled solids referred to as sludge. Blending experiments were performed in a 2.44 meter diameter pilot scale tank, and flow rate measurements and settling tests were performed at both pilot scale an...

Water hammer pressure waves induce oscillating bands of high stresses along pipes, where fatigue ... more Water hammer pressure waves induce oscillating bands of high stresses along pipes, where fatigue corrosion accelerates at bands of localized high stress. Coined as tiger stripes, fatigue corrosion forms at nearly equidistant locations along the bore of piping. For this study, as manufactured A106 carbon steel piping, with intact mill scale, was examined both visually and with a scanning electron microscope (SEM, Zeiss, Gemini 500). The piping for this study was damaged by water hammer with thousands of scratch-like visible cracks with coupled corrosion, and millions of microscopic cracks were discovered during this research. Some piping experienced corrosion bands, and some did not, where these differences in corrosion mechanics are discussed in a Part I of this series. For comparison to piping fatigue corrosion, an as-manufactured, carbon steel flat bar with intact mill scale was investigated. The mill scale was removed with a grinder, and this sample was corroded in a saturated salt solution at 20 °C. As expected, the base metal was not significantly cracked, even after extensive corrosion. However, the corrosion products, or rust deposits, were cracked in numerous locations. In short, water hammer cracks piping, and cracks induce crevice corrosion to shorten the lives of piping systems. This study provides an extensive SEM photographic library to concisely explain and understand fatigue corrosion. Although I reviewed far more photographs than are presented here, one goal of this work is to permit the reader to comprehensively visualize the results that were discovered. What I see is what I want others to see, where this work is applicable to corrosion, piping, structural, and fluids engineering.

This study focuses on fatigue corrosion. The different process of corrosion fatigue is a long-sta... more This study focuses on fatigue corrosion. The different process of corrosion fatigue is a long-standing field of study, where corrosion induces cracks. This research study presents cases where cyclic fatigue cracks surface coatings to induce crevice corrosion. As specific case studies, carbon steel and cast-iron piping failures were researched, cyclic stresses cracked the mill scale or coating, and crevice corrosion and under-deposit corrosion initiated under the mill scale or coating. Similarly, cracks in other protective coatings will cause fatigue corrosion as well. In fact, corrosion engineers have long believed that corrosion is the primary cause of water hammer piping cracks, but the reverse is true. Water hammers provide the cyclic stresses to initiate fatigue corrosion. The American Society of Mechanical Engineers publishes fatigue curves for cyclic loads, and one of those curves was used to show that fatigue corrosion inside piping or fatigue induced failures in the absence of corrosion inside piping, induce failures at about the same time. However, water hammer induced fatigue corrosion causes far more visible damage due to the excessive pitting, while fatigue simply cracks pipes. Either way, piping fails prematurely when hammered due to excessive pressures and dynamic stress effects. In short, piping systems are frequently designed incorrectly when water hammers occur during operations.

This study focuses on fatigue corrosion. Corrosion fatigue is a long-standing field of study, whe... more This study focuses on fatigue corrosion. Corrosion fatigue is a long-standing field of study, where corrosion induces cracks. This research presents cases where cyclic fatigue cracks surfaces and surface coatings to induce crevice corrosion. As a case study, carbon steel and cast-iron piping failures were researched, cyclic stresses cracked the mill scale or coating, and crevice corrosion and underdeposit corrosion initiated under the mill scale or coating. Similarly, cracks in other protective coatings will cause fatigue corrosion as well. In fact, corrosion engineers have long believed that corrosion is the primary cause of piping cracks, but the reverse is true. Water hammer models provide the pressures, where the number of cyclic stresses to initiate fatigue corrosion were observed in service. For one case study considered here, the dynamic stresses were near 13,000 psig in a 1510 psig system. Even though fatigue cycles are consistent with published ASME B31 fatigue curves, the piping stresses were well above design pressures. Cracks and leaks were expected whether or not corrosion initiated. That is, crevice corrosion was greatly increased to increase surface damages, but the rate of fatigue failure was unaffected for carbon steel. Given this new information, piping systems are incorrectly designed when water hammers occur during operations.

International Journal of Philosophy, 2021
Due to misdiagnosed hydrogen explosions and ethically flawed publications, nuclear power plants a... more Due to misdiagnosed hydrogen explosions and ethically flawed publications, nuclear power plants are not as safe as published to be for decades. Previous publications inaccurately, unethically, and inappropriately assessed reactor safety with respect to other industries and natural disasters, where nuclear industry publications non-conservatively applied data to promote nuclear reactor safety, and published models skewed accident data to present nuclear energy as safer than it is. Major findings of this one-man study were calculated with 95% confidence. 1) Explosions caused by fluid transients accompany nuclear power plant meltdowns. 2) A meltdown similar to Three Mile Island (TMI-2) has a 50% probability before 2039, with a one in two probability of a radioactive release like Fukushima. 3) A large radioactive release like Fukushima has a 50% probability before 2067. 4) Radioactive releases can be prevented by fluid transient control with the exception of Chernobyl type accidents, wh...
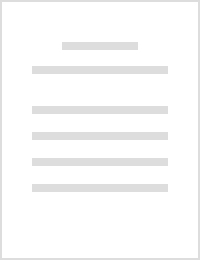
Process Industries, 2005
A reduction of vibrations in mechanical seals increases the life of the seals in centrifugal pump... more A reduction of vibrations in mechanical seals increases the life of the seals in centrifugal pumps by minimizing fatigue damage. Mechanical seals consist of two smooth seal faces. one face is stationary with respect to the pump. The other rotates. Between the faces a fluid film evaporates as the fluid moves radially outward across the seal face. ideally, the film evaporates as it reaches the outer surface of the seal faces, thereby preventing leakage from the pump and effectively lubricating the two surfaces. Relative vibrations between the two surfaces affect the fluid film and lead to stresses on the seal faces, which lead to fatigue damage. As the fluid film breaks down impacts between the two seal faces create tensile stresses on the faces, which cycle at the speed of the motor rotation. These cyclic stresses provide the mechanism leading to fatigue crack growth. The magnitude of the stress is directly related to the rate of crack growth and time to failure of a seal. Related to the stress magnitude, vibration data is related to the life of mechanical seals in pumps.

Volume 6: Fluids and Thermal Systems; Advances for Process Industries, Parts A and B, 2011
Research has been completed in a pilot scale, eight foot diameter tank to investigate blending, u... more Research has been completed in a pilot scale, eight foot diameter tank to investigate blending, using a pump with dual opposing jets. The jets re-circulate fluids in the tank to promote blending when fluids are added to the tank. Different jet diameters and different horizontal and vertical orientations of the jets were investigated. In all, eighty five tests were performed both in a tank without internal obstructions and a tank with vertical obstructions similar to a tube bank in a heat exchanger. These obstructions provided scale models of several miles of two inch diameter, serpentine, vertical cooling coils below the liquid surface for a full scale, 1.3 million gallon, liquid radioactive waste storage tank. Two types of tests were performed. One type of test used a tracer fluid, which was homogeneously blended into solution. Data were statistically evaluated to determine blending times for solutions of different density and viscosity, and the blending times were successfully com...

Oxygen and air mixing with spargers was performed in a 30 foot tall by 30 inch diameter column, t... more Oxygen and air mixing with spargers was performed in a 30 foot tall by 30 inch diameter column, to investigate mass transfer as air sparged up through the column and removed saturated oxygen from solution. The mixing techniques required to support this research are the focus of this paper. The fluids tested included water, water with an antifoam agent (AFA), and a high, solids content, Bingham plastic, nuclear waste simulant with AFA, referred to as AZ01 simulant, which is non-radioactive. Mixing of fluids in the column was performed using a recirculation system and an air sparger. The re-circulation system consisted of the column, a re-circulating pump, and associated piping. The air sparger was fabricated from a two inch diameter pipe concentrically installed in the column and open near the bottom of the column. The column contents were slowly re-circulated while fluids were mixed with the air sparger. Samples were rheologically tested to ensure effective mixing, as required. Once...

Journal of Fluids Engineering, 2010
Mass transfer rates were measured in a large scale system, which is consisted of an 8.4 m tall by... more Mass transfer rates were measured in a large scale system, which is consisted of an 8.4 m tall by 0.76 m diameter column, containing one of the three fluids: water with an antifoam agent, water without an antifoam agent, and AZ101 simulant, which simulated a non-Newtonian nuclear waste. The testing contributed to the evaluation of large scale mass transfer of hydrogen in nuclear waste tanks. Due to its radioactivity, the waste was chemically simulated and due to flammability concerns, oxygen was used in lieu of hydrogen. Different liquids were used to better understand the mass transfer processes, where each of the fluids was saturated with oxygen, and the oxygen was then removed from the solution as air bubbled up or sparged through the solution from the bottom of the column. Air sparging was supplied by a single tube, which was co-axial to the column; the decrease in oxygen concentration was recorded, and oxygen measurements were then used to determine the mass transfer coefficien...

Flow evolution models were developed to evaluate the performance of the new advanced design mixer... more Flow evolution models were developed to evaluate the performance of the new advanced design mixer pump (ADMP) for sludge mixing and removal operations in one of the large-scale Savannah River Site (SRS) waste tanks, Tank 18. This paper is the first in a series of four that describe the computational model and its validation, the experiment facility and the flow measurements used to provide the validation data, the extension of the computational results to real tank conditions through the use of existing sludge suspension data, and finally, the sludge removal results from actual Tank 18 operations using the new ADMP. A computational fluid dynamics (CFD) approach was used to simulate the sludge removal operations. The models employed a threedimensional representation of the tank with a two-equation turbulence model, since this approach was verified by both test and literature data. The discharge of the ADMP was modeled as oppositely directed hydraulic jets submerged at the center of t...

American Society of Mechanical EWngineers,, Mechanicl Engineering Magazine, 2013
Computational fluid dynamics is recognized as a powerful engineering tool. That is, CFD has advan... more Computational fluid dynamics is recognized as a powerful engineering tool. That is, CFD has advanced over the years to the point where it can now give us deep insight into the analysis of very complex processes. There is a danger, though, that an engineer can place too much confidence in a simulation. If a user is not careful, it is easy to believe that if you plug in the numbers, the answer comes out, and you are done. This assumption can lead to significant errors. As we discovered in the course of a study on behalf of the Department of Energy's Salt Disposition Integration Project at the Savannah River Site in Aiken, S.C., CFD models fail to capture some of the large variations inherent in complex processes. These variations, or scatter, in experimental data emerge from physical tests and
are inadequately captured or expressed by calculated
mean values for a process. This anomaly between
experiment and theory can lead to serious errors in
engineering analysis and design unless a correction
factor is experimentally validated. For this study,
blending times for the mixing of salt solutions in large
storage tanks were the process of concern. Radioactive liquid waste is stored at the Savannah River Site in 47 underground storage tanks that vary in capacity from 850,000 to 1.3 million gallons.
ASME Mechanical Engineering Magazine, 2014
It can be hard to get even scientifically minded people to reexamine their conclusions; change is... more It can be hard to get even scientifically minded people to reexamine their conclusions; change is hard to hold on to. I have been working toward acceptance of a new theory of mine concerning accidental combustion in nuclear facility and oil industry pipelines. The theory has safety implications for any pipeline where explosive gases can form in
liquid filled systems, and is consistent with pipeline accidents in nuclear
power plants, such as Three Mile Island. (revised since initial publication)

Mechanical Engineering
This article focuses on various aspects of research theory and development work concerning accide... more This article focuses on various aspects of research theory and development work concerning accidental combustion in nuclear facility and oil industry pipelines. The theory has safety implications for any pipeline where explosive gases can form in liquid-filled systems, and is consistent with pipeline accidents in nuclear power plants, such as Three Mile Island. Nuclear reactor accidents deserve further investigation, since reactor fires and explosions were ignited by sources that were reported to be unknown. The NRC documented extensive actions to improve reactor safety after the Three Mile Island accident; however, this new ignition theory has yet to be fully evaluated with respect to off-normal reactor operations in the United States and abroad. Several nuclear reactor fires and explosions warrant consideration. This new theory confirms a source of ignition. Reactor explosions can be stopped to improve nuclear reactor safety, prevent deaths, and avoid environmental disasters.

Westinghouse Savannah River Company, 2005
The reliability of telescopic transfer pumps is expected to be affected by vibrations which lead ... more The reliability of telescopic transfer pumps is expected to be affected by vibrations which lead to mechanical seal failures. Similar pumps with identical problems last 1000 to 2000 hours left uncorrected. Changing the operating speeds or modifying the bearings are the principle corrective actions that have been evaluated. For pumps already installed in nuclear waste tanks, bearing changes are not an option. The required operating speeds of some pumps may prevent speed changes, but the reliability of other pumps can be improved by speed changes. In particular, the high capacity pumps on Tanks 40 and 51 can have their speeds reduced from 2100 to 2000 rpm. This change is recommended since the pump seal failed. The Tank 51 transfer pump was operated
in excess of 750 hours at acceptable speeds of 1950 to 2000 rpm, and then operated for ten hours at 2100 rpm near one of the pump’s critical speeds. High vibrations at this speed damaged the lower mechanical seal, which leaked water into a waste tank at a rate that could not be corrected. The pump was replaced.

Westinghouse Savannah River Company, 2005
The Evaporator Feed Pump (EFP) is the first long shaft vertical pump with water lubricated carbon... more The Evaporator Feed Pump (EFP) is the first long shaft vertical pump with water lubricated carbon journal bearings to operate with any degree of reliability at the Savannah River Site (SRS). Several pumps of similar design are operated in radioactive waste tanks throughout the H and F Area Tank Farms. These other pumps have developed mechanical seal leaks within 1000 hours, unless the pumps were improved. The EFP has operated in excess of 13,000 hours, and continues to run.
Controlled operating speeds are the principle difference between the EFP and the other pumps. That is, the pump is not operated at speeds which excite high vibrations and damage the seals. Also, the EFP was modified following seal failures during initial testing. The seal design was changed to improve cooling of the seal, and one of the bearings was redesigned to reduce vibration at the seal. While these improvements potentially increased seal reliability, operating the pump at increased vibration levels will reduce seal life. Speed control of the pumps resulted in increased reliability.
Westinghouse Savannah River Company, 2005
The Standard Slurry Pumps are expected to be unreliable, and improvements have not been pursued. ... more The Standard Slurry Pumps are expected to be unreliable, and improvements have not been pursued. There are presently six operating pumps, and one additional pump. Four of these pumps have operated for 2500 hours, and one has failed due to a mechanical seal leak. Two other pumps have operated for 1800 hours, and one has failed due to a seal leak. The additional seventh pump has been tested for vibration, and has significant vibration expected to lead to pump damage. Vibration damage can be minimized by changing the bearings and the impeller or lowering operating speeds. If the bearings are modified, further analysis is required to ensure that the lower shaft diameter is adequate.
Uploads
Papers by Robert Leishear
Water Main Breaks are a Trillion Dollar Wreck. There are $15 billion per year in U.S. and Canadian water main breaks. 250,000 water main breaks per year in U.S. and Canada. Replacement costs are $1 million per mile. $1 trillion in water main breaks in the next 25 years.
are inadequately captured or expressed by calculated
mean values for a process. This anomaly between
experiment and theory can lead to serious errors in
engineering analysis and design unless a correction
factor is experimentally validated. For this study,
blending times for the mixing of salt solutions in large
storage tanks were the process of concern. Radioactive liquid waste is stored at the Savannah River Site in 47 underground storage tanks that vary in capacity from 850,000 to 1.3 million gallons.
liquid filled systems, and is consistent with pipeline accidents in nuclear
power plants, such as Three Mile Island. (revised since initial publication)
in excess of 750 hours at acceptable speeds of 1950 to 2000 rpm, and then operated for ten hours at 2100 rpm near one of the pump’s critical speeds. High vibrations at this speed damaged the lower mechanical seal, which leaked water into a waste tank at a rate that could not be corrected. The pump was replaced.
Controlled operating speeds are the principle difference between the EFP and the other pumps. That is, the pump is not operated at speeds which excite high vibrations and damage the seals. Also, the EFP was modified following seal failures during initial testing. The seal design was changed to improve cooling of the seal, and one of the bearings was redesigned to reduce vibration at the seal. While these improvements potentially increased seal reliability, operating the pump at increased vibration levels will reduce seal life. Speed control of the pumps resulted in increased reliability.
Water Main Breaks are a Trillion Dollar Wreck. There are $15 billion per year in U.S. and Canadian water main breaks. 250,000 water main breaks per year in U.S. and Canada. Replacement costs are $1 million per mile. $1 trillion in water main breaks in the next 25 years.
are inadequately captured or expressed by calculated
mean values for a process. This anomaly between
experiment and theory can lead to serious errors in
engineering analysis and design unless a correction
factor is experimentally validated. For this study,
blending times for the mixing of salt solutions in large
storage tanks were the process of concern. Radioactive liquid waste is stored at the Savannah River Site in 47 underground storage tanks that vary in capacity from 850,000 to 1.3 million gallons.
liquid filled systems, and is consistent with pipeline accidents in nuclear
power plants, such as Three Mile Island. (revised since initial publication)
in excess of 750 hours at acceptable speeds of 1950 to 2000 rpm, and then operated for ten hours at 2100 rpm near one of the pump’s critical speeds. High vibrations at this speed damaged the lower mechanical seal, which leaked water into a waste tank at a rate that could not be corrected. The pump was replaced.
Controlled operating speeds are the principle difference between the EFP and the other pumps. That is, the pump is not operated at speeds which excite high vibrations and damage the seals. Also, the EFP was modified following seal failures during initial testing. The seal design was changed to improve cooling of the seal, and one of the bearings was redesigned to reduce vibration at the seal. While these improvements potentially increased seal reliability, operating the pump at increased vibration levels will reduce seal life. Speed control of the pumps resulted in increased reliability.
I had already published theory to explain the Fukushima explosions before those explosions blasted into the air. When the explosions were first televised, I stated to my wife that “They just turned on the pumps”. The technology was already invented to prevent those explosions.
The next nuclear power plant explosion is on the way, and expected world-wide radiation clouds and cancer deaths can be stopped if action is taken before this explosion blasts into our lives. Changing public opinion to make our world safer is the next step in this one-man challenge to the nuclear industry.